Soluciones para Equipo Estacionario
Procesamiento Químico
Las plantas de procesamiento químico de todo el mundo recurren a Chesterton para satisfacer y superar los requisitos de emisiones fugitivas, solucionar desafíos de sellado complejos y aumentar la confiabilidad y seguridad del equipo.
Nuestro personal altamente experimentado local ofrece soluciones de sellado de última generación para equipos estacionarios, junto con una línea completa de galardonada tecnología de empaquetado y sellado de vástago de válvulas. Su planta se beneficia de sistemas de sellado de alto rendimiento para una amplia gama de aplicaciones de procesamiento químico.
- Lograr emisiones de válvulas óptimas y rentables según las normas ISO
- Resuelve los difíciles desafíos de sellado de válvulas rápida y eficazmente
- Aumentar el rendimiento del activo y ampliar la vida del activo
- Mejorar la seguridad de los empleados
- Mejorar el rendimiento de la planta y la rentabilidad global
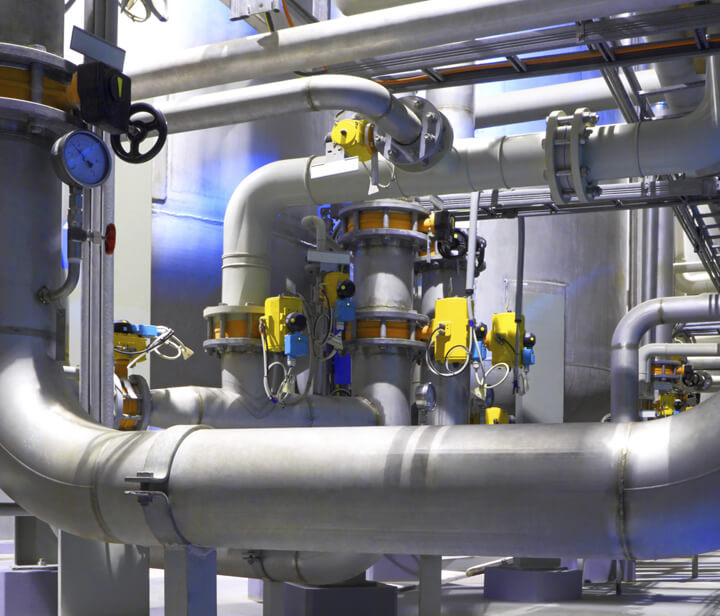
Casos de Estudio
Sellado de Bajas Emisiones Obtenido con Empaque de PTFE
Un gran cliente de la industria química necesitaba un empaquetado de válvula de control capaz de sellar hasta los límites de emisiones permitidos más recientes. Un plan y pruebas fueron requeridos rápidamente.
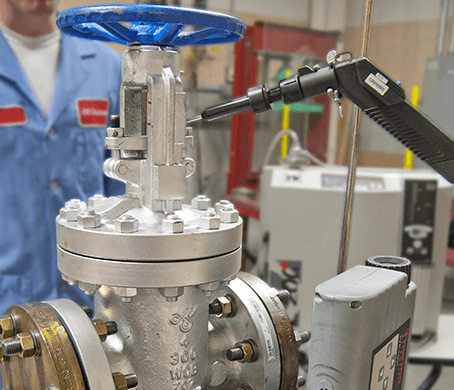
El equipo de Chesterton desarrolló una prueba personalizada basada en protocolos API e ISO adaptados para PTFE. La empaquetadura 1724 con carga viva fue probada.
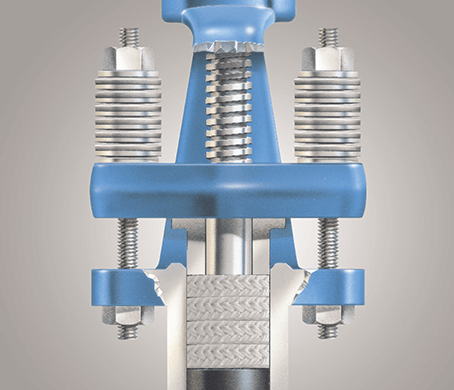
Bajo pruebas, todas las mediciones de fugas estaban muy por debajo de los requisitos permitidos. No se requirieron re-torques.
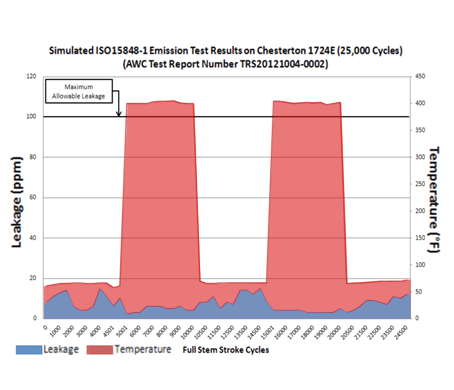
Producto en la Solución
Éxito en la Solución de Bajas Emisiones para las válvulas de Bloque Químico
La planta química necesitaba una solución de embalaje de válvulas rápidamente para cumplir con los nuevos requisitos de emisiones de la EPA. El ensayo se llevó a cabo a una temperatura de 400 ° F (200 ° C).
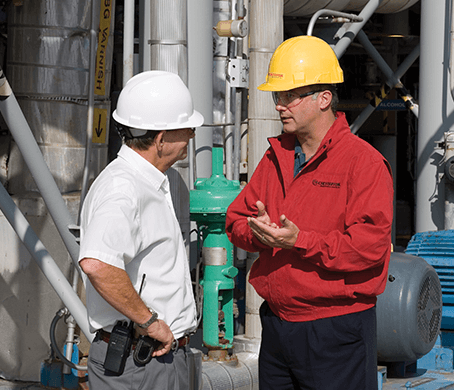
Chesterton desarrolló un protocolo de prueba para evaluar el empaque de PTFE modificando el API. Se utilizó el empaque 1724 con carga viva.
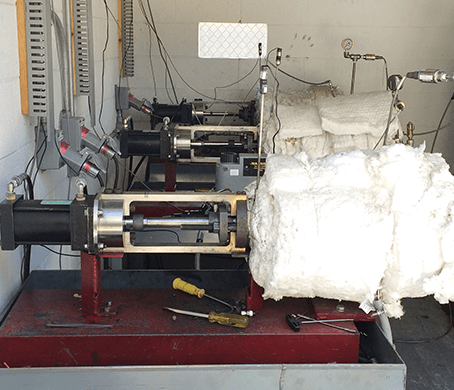
Todas las mediciones de fugas estaban muy por debajo de los requerimientos de 100 ppm. A temperaturas superiores, la fuga varió de 5-10 ppm.
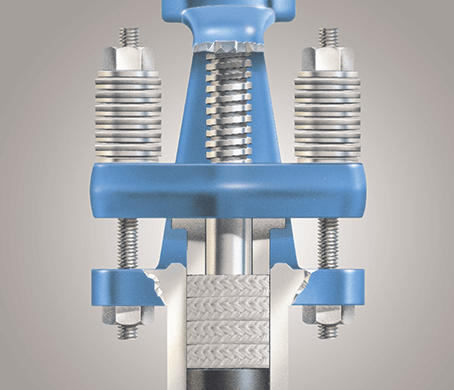
Producto en la Solución
16 Intercambiadores de Calor Restaurados a nuevos
El desempeño del intercambiador de calor se degradó por corrosión y acumulación extensa, exacerbada por el contenido de minerales y cloruros del agua de proceso.
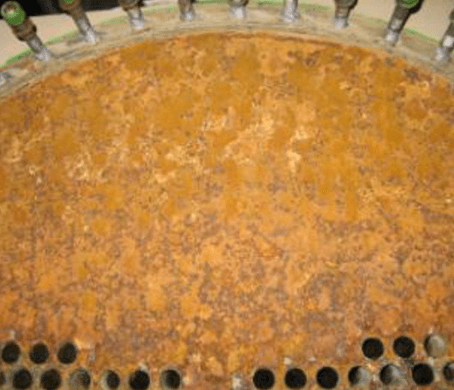
Descontaminar la superficie y aplicar revestimiento reforzado con cerámica ARC 855, para reconstruir y restaurar las caras de los tubos y las cubiertas de los extremos.

Los intercambiadores de calor restaurados se comportaron de forma similar a los nuevos. El cliente no reportó reducción del rendimiento en 24 meses.
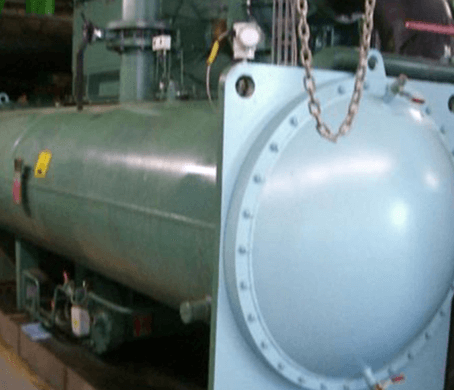
Producto en la Solución