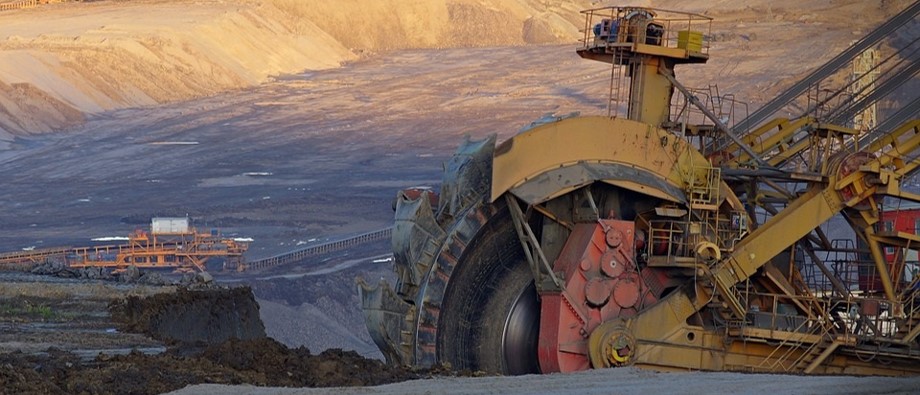
La industria minera y de extracción de mineral es una de las industrias más retadoras al momento de hablar de confiabilidad y mantenibilidad de sus sistemas y equipos (ver “Retos más comunes al sellar lodos/pulpas”).
La cantidad y dureza de sólidos disueltos presentes a lo largo del procesos; el tipo de mezclas químicas generadas para realizar la extracción del mineral, la ubicación geográfica de los centros de explotación minera que, limita la disponibilidad de servicios (como el agua), el valor del fluido sellado y las condiciones mecánicas de las bombas de lodos/pulpas (ver “¿Cuál es la tecnología es más adecuada para sellar lodos/pupas?”) forman parte de las exigencias que debe soportar el sistema de sellado a utilizar en las bombas de lodos/pulpas.
A pesar de las ventajas que genera el uso de sellos mecánicos, la decisión no siempre es tan sencilla cuando se suma el factor económico dentro de la ecuación.
Si bien a largo plazo, el uso de sello mecánico puede ser una inversión que impacta de manera positiva en la mantenibilidad de las bombas de lodos/pulpas; la inversión inicial puede llegar a ser intimidante para los usuarios acostumbrados al uso de empaquetadura. Sobre todo porque los sellos mecánicos de alto desempeño que pueden sobreponerse a las condiciones de operación típicas de una mina, son considerados sellos mecánicos de especialidad.
Un salto no tan arriesgado pero que puede ofrecer beneficios superiores cuando la operación actual de los equipos se ha convertido en un problema critico de confiabilidad y mantenibilidad, es el uso de empaquetaduras de alta tecnología, desarrolladas particularmente para la contención eficiente y confiable de los lodos/pulpas en la industria minera y de extracción de minerales.
Características de las Empaquetaduras para Sellado de Lodos/pulpas.
La herramienta más utilizada para clientes y usuarios al seleccionar una empaquetadura para el sellado de lodos/pulpas es la ficha técnica. En ella se presenta información esencial respecto a los límites mínimos y máximos de temperatura (acotado por el material de construcción y lubricantes), la presión máxima, velocidad periférica y resistencia química expresadas a través de rangos de pH.
Hablar de una empaquetadura de alta tecnología desarrollada para la contención eficiente en el sellado de lodos/pulpas en la industria minera y de extracción de minerales va más allá de comparar los valores operativos en una ficha técnica. Existen propiedades químicas y mecánicas en las empaquetaduras que pueden ser medidas únicamente en operación.
Recordemos que un lodo/pulpa es la combinación de una fase sólida en una fase líquida y que la severidad de un lodo/pulpa se define a través de las siguientes características:
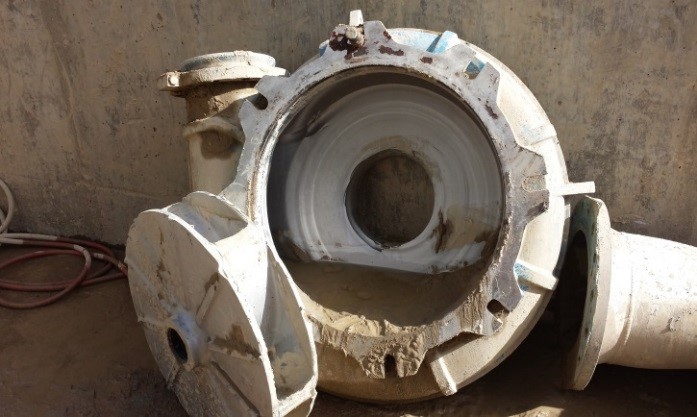
- Geometría de las partículas sólidas
- Tamaño de las partículas sólidas
- Dureza de las partículas sólidas
Estos, pueden ser menos o más agresivo para la bomba de lodos/pulpas de acuerdo a las condiciones ambientales de sellado como:
- La limpieza que podamos alcanzar en la zona de sellado
- La lubricación (propia del fluido)
- La temperatura adecuada (en la mayoría de los casos se requiere un ambiente fresco)
Muchos Lodos/Pulpas además pueden llegar a ser altamente corrosivos incrementando la dificultad al sellarlos.
La combinación de la naturaleza del lodo/pulpa más las condiciones ambientales de operación impactan directamente sobre la confiabilidad del sistema, de manera que los usuarios manifiestan:
- La empaquetadura se quema
- La empaquetadura se extruye
- Desgasta la camisa/eje de manera acelerada
- La empaquetadura se endurece, pierde volumen de manera acelerada
- Se produce fuga en un lapso corto de tiempo
Los principales diferenciadores de las empaquetaduras diseñadas bajo la filosofía de alto desempeño confiable, están relacionadas con la calidad de los materiales, tecnología de las fibras, tipo y mecanismo de lubricación, los procesos de fabricación de la trenza; son claves de diseño que los fabricantes de renombre han desarrollado a través de la experiencia con enfoque en los problemas comunes que agobian a los usuarios de la industria minera y de extracción de minerales.
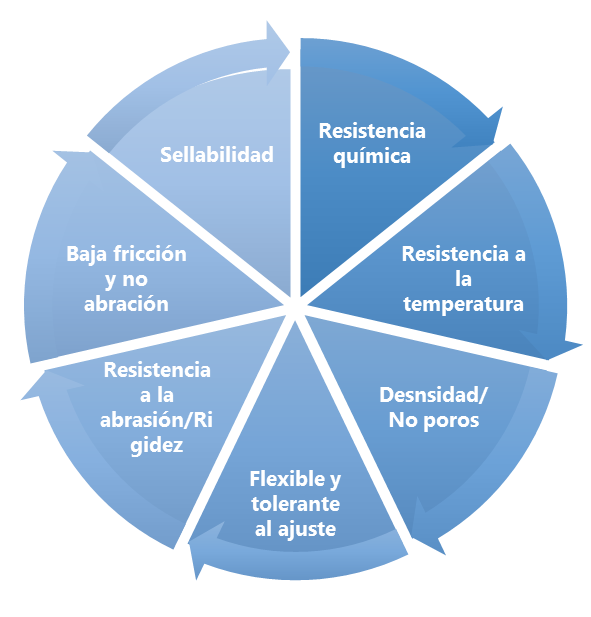
- Resistencia química – soporta el ambiente químico presente en el estopero de una bomba de lodos/pulpa (pulpas cianuradas, productos de lixiviación, soluciones preñadas).
- Resistencia a la temperatura – para soportar la temperatura del o generada por el proceso y por el calor por fricción.
- Densidad y no poros– Evitar la fuga a través de la empaquetadura y evitar la acumulación de sólidos
- Flexible y además tolerante al ajuste – para amoldarse al eje y el estopero y reducir la fuga sin perder consistencia.
- Resistencia a la abrasión y rigidez: Previene la extrusión y deslave, reduce la fricción
- Baja fricción y no abrasión: reduce el consumo de energía, evita calor por fricción, reduce el desgaste en la empaquetadura y el equipo.
- Sellabilidad– Aumenta la confiabilidad del equipo, reduce riesgos de seguridad y de mantenibilidad.
Algunas de las características que hacen la diferencia entre una empaquetadura de alta tecnología desarrollada para la contención eficiente de los lodos/pulpas en la industria minera y de extracción de minerales (señaladas en la figura anterior) respecto a un empaque tradicional, no se pueden mediar mediante la ficha técnica. Estas propiedades químicas y mecánicas en las empaquetaduras de lodos/pulpas deben ser evaluadas bajo un esquema de desgaste acelerado que simule las condiciones de la empaquetadura de lodos/pulpas en operación.
Resistencia Química
¿Qué hace la diferencia?
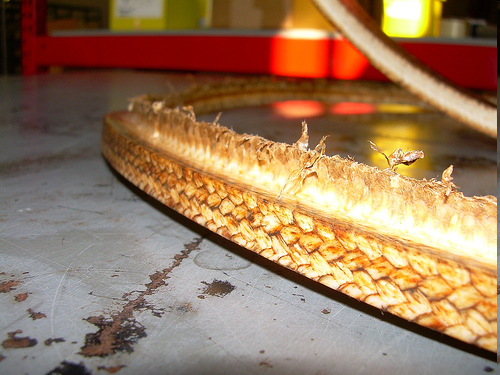
Esta característica reside en la naturaleza del material de construcción y lubricación. Es clave revisar la compatibilidad química de cada una de las materias primas de la empaquetadura, las fibras, los lubricantes o cualquier componente de construcción de las empaquetaduras que entre en contacto con el lodo/pulpa.
Algunos productos químicos, además de acarrear riesgos por sí mismos, son capaces de dar lugar a reacciones peligrosas en contacto con otros. Materiales incompatibles químicamente son aquellos que al ponerse en contacto entre sí sufren una reacción química descontrolada que puede resultar en degradación del empaque y después en fuga de la bomba hacia el medio ambiente.
Resistencia a la temperatura
¿Qué hace la diferencia?
Cada empaquetadura tiene límites de temperatura máxima y mínima. La temperatura máxima depende de los materiales utilizados en la fabricación. Por ejemplo, el grafito tiene un límite de temperatura de 450°C en ambientes oxidantes y 650°C en vapor y ambientes no oxidantes, pero si se lubrica con PTFE, tomará el valor máximo de este, 260°C.
Por un lado, está la resistencia del material a la temperatura del medio bombeado, esto es la temperatura máxima o mínima a la cual el material cambia sus propiedades químicas y mecánicas por estar sumergido en el fluido. Pero, ¿qué pasa con el calor generado entre la empaquetadura y el eje de la bomba? La conductividad térmica es una propiedad física de todos los materiales que mide la capacidad de conducción de calor a través del material.
Cuanto mayor sea su conductividad térmica, un material será mejor conductor del calor. Cuanto menor sea, el material será más aislante.
Para la fabricación de empaquetadura de alta tecnología, desarrollada para la contención eficiente de los lodos/pulpas en la industria minera y de extracción de minerales, se buscan materiales de alta conductividad térmica con el objeto de conducir/encaminar de manera rápida, el calor generado por la fricción entre el eje y la empaquetadura, a través del propio material de la empaquetadura y llevarlo hacia el fluido de bombeo en la caja de esteperos. Esto evitará que no se dañe ni el equipo ni al empaque por un aumento de temperatura tal que pueda alcanzar el límite del material de construcción de la empaquetadura.
Bajo esta premisa, un material aislante como la cerámica no debería utilizarse para la fabricación de empaquetaduras, no obstante, por su bajo costo de producción sigue siendo un material muy utilizado no solo en la industria Minera y de Procesamiento de minerales.
Resistencia a la fricción – No abrasión
¿Qué hace la diferencia?
Material y fibra base, el comportamiento del lubricante en la empaquetadura.
Las fibras naturales como el algodón, el lino y el rayón fueron desarrolladas para el uso de la industria textil, con el paso del tiempo se descubrió que podían ser utilizadas de manera satisfactoria para la fabricación de empaquetaduras. Estas fibras suelen tener un costo bajo y son fáciles de trenzar, no obstante, el coeficiente de fricción que manejan es muy alto, por lo que para reducir la generación de calor, a las empaquetaduras fabricadas con este tipo de fibras se les incorpora una cantidad muy alta de lubricantes líquido para tratar de mantener la temperatura y el desgaste controlados. Conforme el trabajo de la bomba de lodos/pulpas, ese volumen de lubricante comienza a perderse rápidamente dejando el material de la trenza seco y propenso a la temperatura generada por fricción. El mismo efecto ocurre con algunas fibras sintéticas como el acrílico, la fibra de vidrio, fibra cerámica y el asbesto. Este último hace años fue prohibido en el uso industrial y de construcción debido a los efectos adversos que causa a la salud. Sin embargo, no es raro encontrar usuarios que siguen utilizando este material dentro de sus bombas de lodos/pulpas y alrededor de toda su planta por el precio de adquisición bajo que maneja.
Por otro lado, las fibras sintéticas modernas como el PTFE, el carbón, el grafito y las aramidas, tienen características muy particulares que las ayudan a sobrevivir ante los servicios severos de la industria minera y de extracción de minerales por lapsos de tiempo muy prolongados cuando se combinan con los lubricantes adecuados.
A continuación, se enlistan algunas de sus características más importantes del PTFE, Carbón, Grafito y fibras Aramidas.
Fibras de PTFE
El PTFE posee una excelente resistencia química, es utilizado para el manejo de ácidos y bases fuertes de pH de 0-14; sustancias de uso común en la extracción de minerales.
Prácticamente cubre todo el espectro en aplicaciones químicas. Tiene un buen coeficiente de fricción que puede ser mejorado con ayuda de lubricantes específicos.
Es de naturaleza auto lubricante hasta cierto límite de velocidad y puede soportar hasta 260°C.
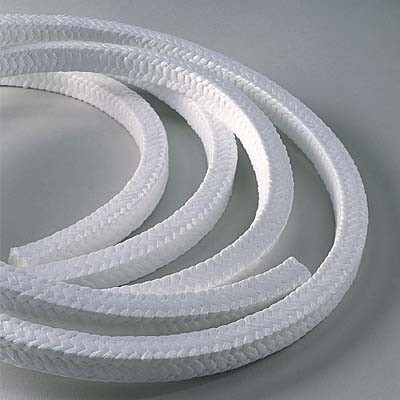
El PTFE virgen sufre de endurecimiento en frio no obstante se han desarrollado formas de reformar estas características inherentes al material, tales como:
- Utilizar Fibras de PTFE de filamento continuas.- Mejora la orientación molecular
- PTFE Expandido (ePTFE)- Se estira y se aplica un tratamiento térmico que incrementa la resistencia y disminuye el endurecimiento
- PTFE con carga: Mejora la tolerancia al esfuerzo y al calor
Fibras de Carbón
Hilo de Grafito, Hilo de Carbón
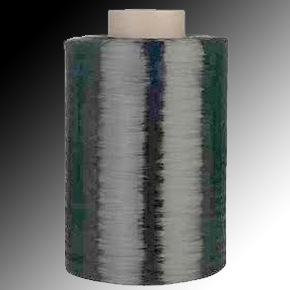
La facilidad de trenzado del hilo de grafito y de carbón hace que la trenza resultante sea más flexible y se pueda conformar mejor en la caja de la bomba.
Es un material sensible por lo que tiene propiedades de sellado moderada.
Un alto coeficiente de fricción y una excelente resistencia a las altas temperaturas.
- Facilidad de trenzado
- Propiedades de sellado moderadas
- Coeficiente de fricción bueno
- Resistente a temperaturas Altas
Grafito Expandido
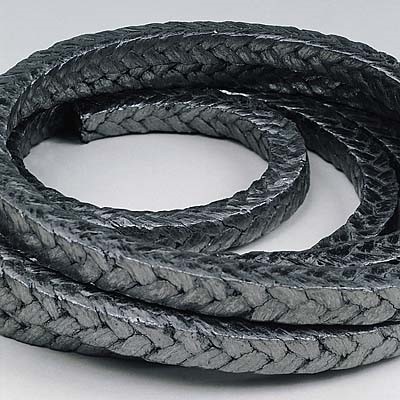
- El grafito expandido se puede utilizar para hacer cinta (grafoil)
- Buenas propiedades de sellado
- Suave
- No abrasivo
- Auto lubricante
- Resistente a temperaturas Altas.
Algunas de las dificultades que se tiene para manejar son:
- Baja resistencia mecánica
- Difícil de trenzar
Fibras de Aramidas: Paramidas y Metaramidas
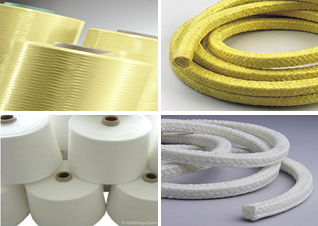
- Alta tenacidad
- Resiliencia
- Resistente a la extrusión


El Lubricante en la Empaquetadura
Existen 2 aspectos fundamentales respecto a los lubricantes utilizados:
- El tipo de lubricante aplicado
- Los lubricantes a base de petróleo como el petrolato y los aceites.
- Lubricantes sintéticos como el PTFE, grafito y silicón.
- La forma de aplicar el lubricante
- A nivel molecular
- Pre lubricado
- Post lubricado
Lubricantes a base petróleo
Comúnmente se utilizan fluidos como el petrolato o algunos tipos de aceites. Este tipo de lubricantes suelen tener un bajo costo de adquisición. Sin embargo, son fluidos que se disipan rápidamente.
Las empaquetaduras que los utilizan suelen incorporar altas cantidades de lubricante para compensar la rápida pérdida del mismo y son aplicados mediante técnicas de inmersión.
Lubricantes sintéticos
Comúnmente se utilizan lubricantes como el PTFE en dispersión, el grafito en forma de hojuelas o dispersión y el silicón.
Este tipo de lubricantes suelen tener un costo de adquisición mayor y son fluidos que tienen mayor resistencia al deslave y a la temperatura, por tanto, suelen permanecer más tiempo activos.
Se aplican mediante técnicas de inmersión o frotamiento y en muchas ocasiones se aplica temperatura para una mejor adherencia y en general son el tipo de lubricante elegido para la fabricación de empaquetadura de alta tecnología desarrollada para la contención eficiente de los lodos/pulpas en la industria minera y de extracción de minerales
Lubricación a nivel molecular
Este tipo de técnica se utiliza con filamentos de PTFE y grafito como lubricante. El grafito es mezclado con el PTFE de forma molecular al preparar la resina que posteriormente será extruida para formar el filamento. La presencia de lubricante es constante y homogénea, por tanto, disminuye el coeficiente de fricción del empaque en todo momento y ayuda a disipar el calor generado de forma más eficiente.
Pre Lubricado
Esta técnica de lubricación consiste en impregnar cada filamento de forma individual previo al proceso de trenzado, en muchas ocasiones se utilizan procesos térmicos para asegurar la adherencia del lubricante al filamento.
El lubricante queda adherido a la superficie del hilo de forma homogénea y con un enlace fuerte que en ocasiones previene la necesidad de un Post Lubricado.
Es una de las mejores técnicas de lubricación para una empaquetadura de alta tecnología desarrollada para la contención eficiente de los lodos/pulpas en la industria minera y de extracción de minerales, no obstante este proceso es más costoso de todos pero conlleva la ventaja de que cuando la empaquetadura es comprimida, el lubricante no se desprende o lo hace de forma mínima, además este proceso permite que el trenzado de la empaquetadura sea más firme.
Los lubricantes más comunes en este proceso son el PTFE y el silicón.
Post lubricado
Esta técnica se aplica el lubricante ya sea por inmersión o por frotamiento.
- Por inmersión:
Cuando el proceso es por inmersión se introduce la empaquetadura ya trenzada en grandes tinas que contienen al lubricante en estado líquido, se deja inmersa la empaquetadura por algún lapso de tiempo definido y posteriormente se retira para verificar que “absorbió” la cantidad de lubricante esperada, en algunos casos posteriormente se introduce la empaquetadura a hornos para generar una mejor adherencia del lubricante.
El resultado de este tipo de proceso es una absorción de gran cantidad de lubricante, pero de forma muy irregular, así mismo el lubricante atrapado al interior de la empaquetadura es fácilmente liberado al comprimir la empaquetadura.
Las empaquetaduras con este tipo de lubricación tienden a sufrir más consolidación (pérdida de volumen). Es un proceso relativamente barato comparado con la Pre lubricación.
- Por Frotamiento
El proceso por frotamiento más utilizado es el “grafitado” el cual consiste en aplicar de forma “externa” una solución a base de hojuelas de grafito ya sea mediante brochas o telas. El resultado de este proceso es una aplicación superficial de grafito que tiende a durar muy poco tiempo.
Los empaques con este tipo de proceso se caracterizan por ser empaques que manchan cualquier superficie que tocan. Es un proceso muy barato que se utiliza en empaquetaduras de muy baja calidad donde se utiliza el grafito como lubricante de sacrificio.

Sellabilidad
Los empaques que requieren ajustes constantes tienen una menor vida útil y provocan desgaste excesivo al eje o camisa, lo cual no solo se traduce en altos costos de productos sino también en pérdida de fluido de proceso, riesgos de seguridad a los técnicos de mantenimiento y ambientes sucios e inseguros alrededor de la bomba.
La fuga del estopero se encuentra en una zona muy cercana al área de los rodamientos del equipo. Altos niveles de fuga regularmente se traducen en contaminación del lubricante de los rodamientos disminuyendo drásticamente su vida útil, este es otro argumento de ventas no solo para la empaquetadura, sino para los protectores de rodamientos.
¿Qué hace la diferencia?
- La flexibilidad, relacionada a la calidad de los materiales y la construcción de la empaquetadura.
- Densidad, no poros
- Tolerancia al ajuste
Flexibilidad
- Los empaques flexibles se conforman de mejor manera al eje disminuyendo las rutas de fuga.
- Se pueden amoldar a las irregularidades y desgaste presente en el eje o camisa.
- Requieren menos compresión en el prensa estopas para controlar adecuadamente al fuga.
- Son más sensibles a la acción de las fuerzas hidráulicas en el estopero.
- Una de las principales preocupaciones con un empaque flexible es su baja resistencia a la extrusión.
- Los hilos de alta gama diseñados específicamente para fabricación de empaquetaduras incorporan una excelente combinación de flexibilidad y resistencia a la tensión.
Construcción
Ya hemos explicado cómo contribuye la calidad de los materiales en el desempeño de una empaquetadura diseñada para trabajar en ambientes agresivos como son las bombas de lodos/pulpas.
Ahora toca hablar de cómo la construcción de la empaquetadura puede hacer una diferencia puntual en desempeño
Los 2 tipos de trenzado más utilizados en la fabricación de empaquetaduras son:
- Trenzado cuadrado (simple)
Este proceso de fabricación consume menos hilo por tanto se utiliza en secciones muy pequeñas o con materiales difíciles de trenzar como el grafito expandido. Permite la absorción de grandes cantidades de lubricante con la desventaja que estos se desprenden fácilmente.
Las empaquetaduras fabricadas con este proceso son menos flexibles debido a que el material está menos consolidado, por tanto también tiene una baja resistencia a la extrusión. Lo que la lleva a sufrir mayor deformación en operación.
- Intertrenzado (supertrezando)
Este proceso de fabricación consume hasta 1.5 veces más hilo que el trenzado cuadrado. Retiene de mejor forma grandes cantidades de lubricante ya que el material queda mejor consolidado, reduciendo el tamaño de los “poros” y aumentando la densidad. Tiende a incrementar la sellabilidad del empaque ya que tiene menos rutas de fuga.
Las empaquetaduras fabricadas con este proceso tienden a ser más flexibles y con alta resistencia a la extrusión y son ideales para el manejo de altas presiones y servicios abrasivos normales en la industria minera y de extracción de minerales.
- Tolerancia al ajuste
Uno de los factores más críticos para conseguir la operación confiable de las empaquetaduras es lograr el ajuste correcto del prensaestopas, tanto al inicio de la operación como durante el trabajo de la misma. Lograr el ajuste adecuado es un punto complejo que en muchas ocasiones requiere de gran experiencia de quien lleva a cabo la instalación, adicionalmente el ajuste inicial requiere en muchas ocasiones que se tenga un adecuado monitoreo de la fuga y se hagan ajustes secuenciales, lo cual suele ocasionar conflicto con las prácticas operativas del cliente.
El resultado es el sobreajuste de la empaquetadura, llevándolo a fallas catastróficas o a la disminución considerablemente de la vida útil de la empaquetadura. Los usuarios se acostumbran a vivir con esta situación sin embargo, esto implica a la larga una disminución en la confiabilidad, aumento de tiempo y costo de mantenibilidad.
Si bien el ajuste es un factor totalmente ligado la experiencia del instalador (factor humano), existen empaquetaduras que por su diseño, construcción y selección de materiales pueden ser más tolerantes a las malas prácticas de ajuste de manos inexpertas.
En una época donde pareciera no existir diferencia entre un producto (en la ficha técnica) y otro, conocer los principales diferenciadores de las empaquetaduras diseñadas bajo la filosofía de alto desempeño confiable, cómo se relacionan con la calidad de los materiales, la tecnología de las fibras, el tipo y mecanismo de lubricación, los procesos de fabricación para hacer un dispositivo de sellado de alta tecnología capaz de resistir ambientes de sellado agresivo como los encontrados en La industria minera y de extracción de mineral; hace la diferencia entre ofrecer soluciones integrales que generen ahorros y mejores prácticas operativas .
Si desea ayuda para seleccionar la mejor tecnología en empaquetaduras para una aplicación específica, no dude en ponerse en contacto con nuestro servicio Pregunte a un Experto
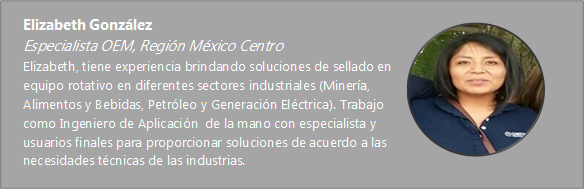
1 comentario
Buenos dias .
Ing Elizabeth .
Excelente artIculo .
Muchas Gracias .